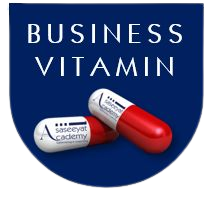
Five Whys
Unpredicted problems may occur in any team or process. However, problems are just symptoms of deeper issues. Fixing a problem quickly may be a convenient solution, however, it doesn’t protect your work process from recurring mistakes. The 5 Whys technique is one of the most effective tools for root cause analysis in the Lean management arsenal. The 5 Whys will help you find the root cause of any problem and protect the process from recurring mistakes and failures. The 5 Whys method was part of the Toyota Production System and was developed by Sakichi Toyoda.